1. 传统工业控制软件为何难以适应智能时代?
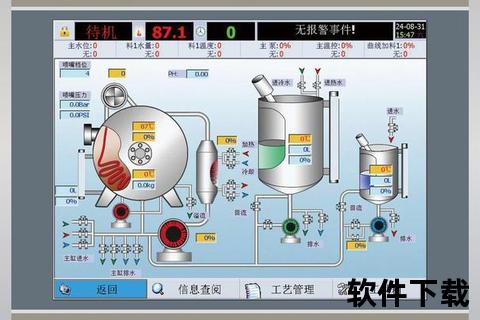
当某汽车零部件工厂在2022年试图升级产线时,工程师发现原有控制系统无法接入新型协作机器人,导致整条产线停工三周——这种场景正在全球制造业频繁上演。据国际自动化协会统计,67%的企业在数字化转型中遭遇过控制系统与智能设备不兼容的问题。面对工业4.0浪潮,"卓越掌控Codesys软件 开启工业自动化智能新纪元"的呼声为何愈发强烈?
在江苏某智能装备制造基地,技术人员通过Codesys V3.5版本成功将西门子PLC、ABB机械臂和国产视觉检测系统整合在统一平台。项目负责人李工透露:"过去需要5种不同编程语言协作的任务,现在通过IEC 61131-3标准实现了代码复用率提升40%。"这印证了德国弗劳恩霍夫研究所的兼容性突破可使产线改造周期缩短60%。
2. 如何让编程效率追上设备迭代速度?
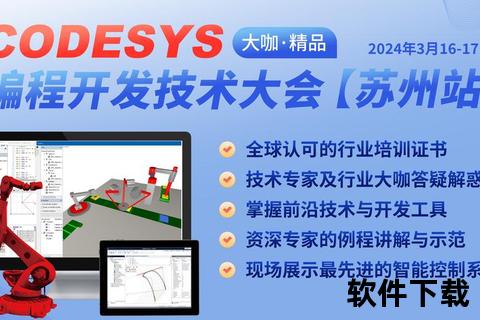
广东某食品包装企业曾因设备程序更新滞后导致新品上市延误,每月损失超300万元订单。其痛点在于:传统梯形图编程修改一个机械手动作需要重新验证整套逻辑。而采用Codesys的运动控制模块后,工程师通过"拖拽式功能块"在3天内完成了原本需要6个月的产线重组。
更值得关注的是其云编译功能带来的变革。山东某工程机械厂商借助Codesys远程开发平台,使分布在德国、重庆、青岛的三支技术团队能实时协作调试液压控制系统。数据显示,这种模式使程序调试时间从平均28天压缩至7天,错误率降低75%。国际工控查显示,采用模块化编程工具的企业研发效率普遍提升2-3倍。
3. 智能化决策能否从实验室走进车间?
内蒙古某风电场运维团队过去每月需要人工分析3.6TB运行数据,现在通过Codesys的OPC UA接口和AI算法库,实现了叶片故障预测准确率91%的突破。这个案例揭示了工业软件的新战场:将边缘计算与云端智能深度融合。
更前沿的应用出现在半导体领域。上海某芯片制造厂在Codesys平台上开发出自适应温控系统,能根据光刻机实时工况动态调整冷却策略,使晶圆良品率提升1.2个百分点。按照每片晶圆2000美元计算,单条产线年增收超过800万美元。这些实践正在验证:"卓越掌控Codesys软件 开启工业自动化智能新纪元"不仅是口号,更是生产力革命。
通往智能制造的务实选择
对于考虑转型的企业,建议分三步走:首先评估现有设备通讯协议支持度(重点关注OPC UA、PROFINET覆盖率),其次组建跨学科的Codesys技术团队(建议配置20%的IT人才),最后从局部产线试点开始(优先选择故障率高或工艺复杂的环节)。
日本三菱重工的转型经验值得借鉴:他们用18个月分阶段部署Codesys,最终实现全厂设备数据打通,意外停机时间减少42%。正如国际自动化学会主席托马斯·鲍尔所言:"未来的工厂不是由最昂贵的设备构成,而是由最具兼容性的大脑连接。"选择"卓越掌控Codesys软件 开启工业自动化智能新纪元",本质上是选择构建面向未来的工业神经系统——这不仅关乎效率提升,更是决定企业能否在智能化浪潮中掌握话语权的战略抉择。
文章已关闭评论!