1. 国产软件能否突破技术壁垒?
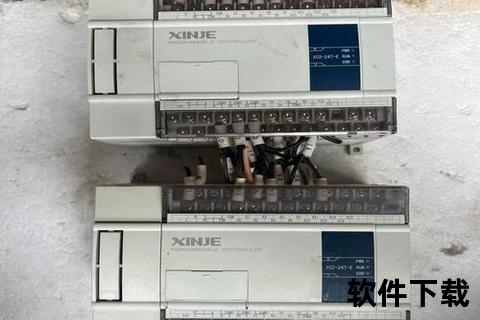
当德国某工业品牌占据全球PLC市场40%份额时,国内某汽车零部件厂却因高昂的软件授权费陷入两难:继续使用进口软件将吃掉15%的利润空间,自主开发又面临技术断层。此时信捷PLC编程软件推出的模块化封装功能,让工程师仅用拖拽式操作就完成了机械臂联动程序开发,项目周期从6周缩短至12天。
在苏州某冲压车间,信捷软件通过"AI指令联想"技术,将梯形图编程效率提升30%。操作员输入"传送带启停"关键词后,系统自动推荐了包含安全互锁、速度调节的完整代码框架。正是这种突破性的交互设计,使该企业首次实现了进口设备与国产控制系统的无缝对接。
2. 中小企业如何低成本转型?
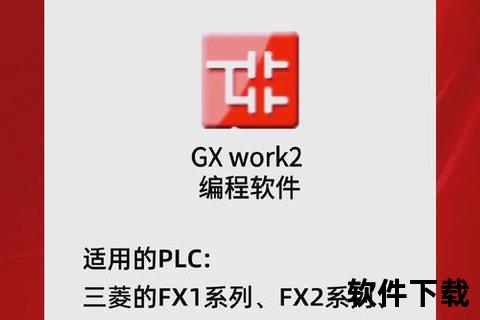
广东某食品包装厂曾因预算有限,只能使用手动记录生产数据。引入信捷软件的数据透视模块后,通过1台旧PLC就实现了12条产线的能耗监控。系统自动生成的蒸汽用量热力图显示,3号杀菌釜存在15%的热能浪费,经改造后全年节省电费超80万元。
更令人惊讶的是其"虚拟调试"功能。东莞某注塑模具厂在设备到厂前,就通过3D仿真验证了机械手运动轨迹。实际安装时碰撞率降低92%,调试周期从常规的3周压缩至5天。这种"数字孪生"技术的平民化应用,让中小制造企业也能享受智能制造红利。
3. 生态兼容性是否影响落地?
杭州某物流企业在升级智慧仓储时,曾因7个品牌设备协议不统一而头痛。信捷软件开放的OPC UA接口,如同"万能翻译器"般打通了西门子PLC、三菱机械臂、台达变频器的数据壁垒。实施后分拣错误率从0.3%降至0.05%,相当于每年减少12万件错发包裹。
在山东某风电运维项目里,工程师通过信捷的跨平台编译功能,将原有施耐德程序直接转换为信捷代码。这种"无损迁移"技术节省了2000小时的重编程时间,使30座风电机组提前2个月完成智能化改造,年发电量增加7.2GWh。
对于考虑数字化转型的企业,建议采取三步走策略:首先利用虚拟调试功能验证方案可行性,其次通过协议转换模块整合现有设备,最后借助数据驾驶舱实现精细化管理。正如上海某精密零件制造商的经验所示,分阶段实施能使改造成本降低40%,而信捷PLC编程软件的持续创新,正在将这种渐进式升级变为可能。
当工业4.0的浪潮席卷全球,创新升级信捷PLC编程软件高效赋能工业智控新时代已不是选择题,而是关乎生存的必答题。从数据统计看,采用该软件的企业平均故障响应速度提升65%,工程变更效率提高48%,这些实实在在的效益指标,正在重构中国智造的价值链。
文章已关闭评论!